Challenges in the Power Grid
The United States’ current power grid infrastructure is grappling with the challenges of transitioning to renewable energy sources. The American Society of Civil Engineers (ASCE) rates our existing infrastructure at a concerning grade of C-. This underperformance, coupled with a lack of robust transmission infrastructure to move large amounts of power around the country, underscores the urgent need for innovation. EarthGrid’s patented plasma-powered technology allows for exponentially faster boring, at a fraction of the cost.
Plasma Tunnel Boring Technology
To comprehend the innovation behind EarthGrid’s technology, it is essential to delve into the mechanics of tunnel boring. Traditional methods involve the use of mechanical drills, but EarthGrid’s approach employs torches powered by plasma created from electricity and airflow. This plasma torch reaches temperatures in the realm of thousands of degrees Celsius, which enables the machines to bore rapidly through various geological formations via vaporization and spallation. The machines’ ability to operate at various depths underground is a key advantage, allowing them to navigate beneath the existing maze of underground utilities.
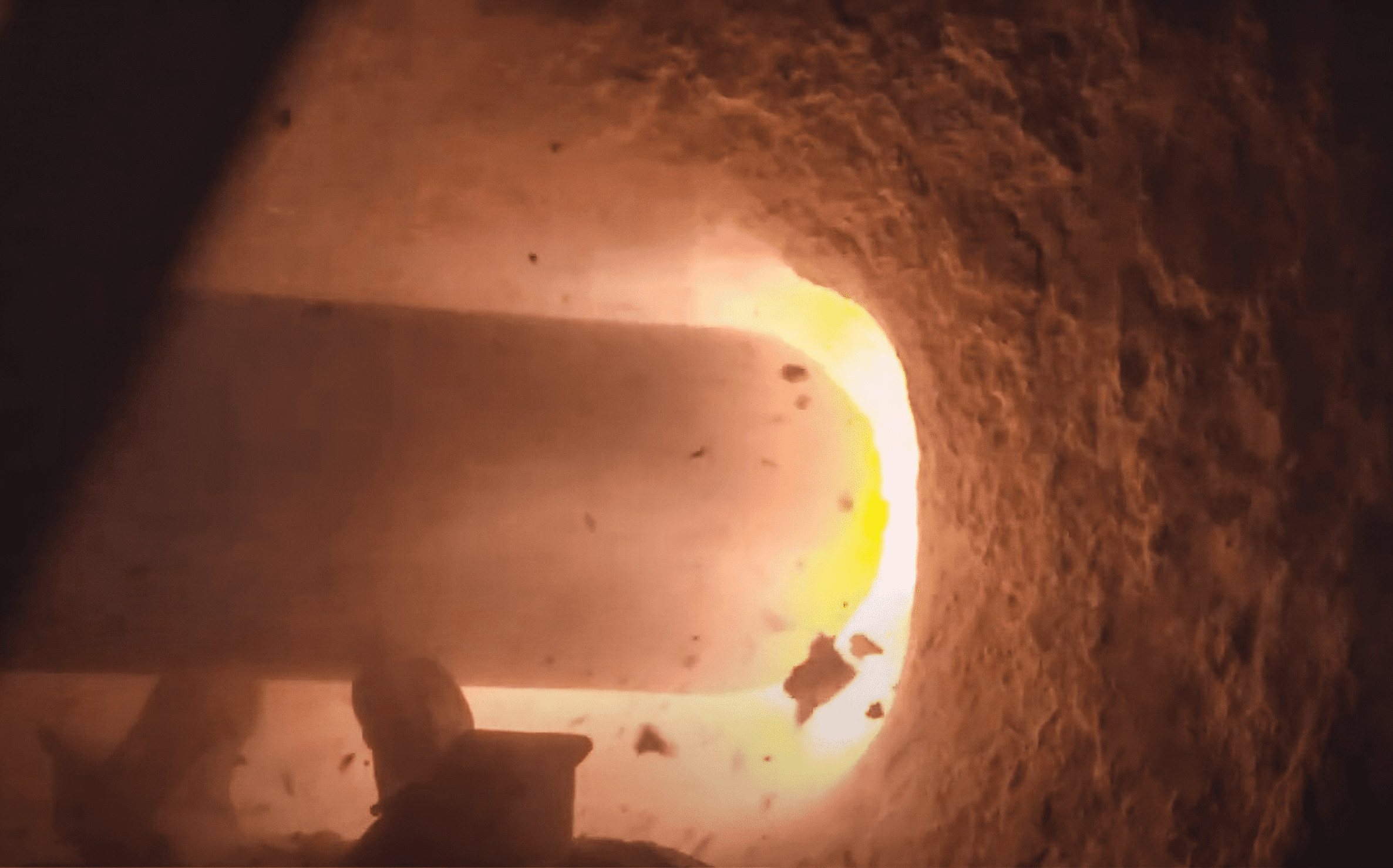
Advantages of Plasma Boring
The speed and cost-effectiveness of EarthGrid’s plasma drilling technology stem from its adaptability to diverse geologies without slowing down. Conventional methods can experience delays when confronted with different terrains, and often complete abandonment of projects due to the degree of difficulty, adding increasing costs that render the projects unfeasible. EarthGrid’s plasma torches, however, boast the capability to bore through various materials seamlessly, by utilizing specialized “Rock Recipes” that allow them to break down the specific type of rock encountered more efficiently.
The cost-effectiveness of EarthGrid’s technology is further exemplified by lower operating costs compared to traditional methods. There is no need for frequent changes of drill bits and cutter heads, resulting in reduced downtime. The absence of drilling mud and chemicals simplifies the waste disposal process and makes the construction less damaging to the surrounding environment.
Addressing Safety and Environmental Concerns
One notable concern surrounding plasma drilling is the extreme heat generated by the process. However, EarthGrid has implemented sophisticated measures to manage this heat effectively. Ground-penetrating radar is employed to meticulously map the underground infrastructure, ensuring that the plasma torches avoid existing utilities and structures.
The heat generated during plasma drilling dissipates through a phase change when the rock melts, resulting in tunnel walls that typically have temperatures below 100 degrees Celsius soon after the torch passes through. This is crucial, as it ensures that the heat is not intense enough to melt pipes or significantly impact the surrounding environment. Furthermore, the utilization of a vacuum removal system and air jets helps dissipate the heat efficiently, minimizing its impact on the surrounding areas.
Versatility Across Geologies
EarthGrid’s plasma drilling technology has undergone extensive testing across a variety of geological conditions, showcasing its adaptability and efficiency. Notably, the technology has demonstrated exceptional speed, surpassing traditional boring techniques, especially when dealing with harder geologies.
In instances where the drilling encounters soil, such as glacial fill-ins, EarthGrid’s technology proves its versatility. The rapid vaporization of organics leaves a crust that can be managed through additional construction techniques, such as ‘shotcreting’ the tunnel walls. The technology has been successfully tested in wet soil, mixed surfaces, and soil with natural gas injections.
Innovative Business Models
EarthGrid introduces two innovative business models—BOOM (Build, Own, Operate & Maintain) and BADASS (Boring And Drilling As a Simple Service)—providing clients with flexibility in project engagement. The BOOM model allows EarthGrid to build and own the tunnel (covering permitting and financing), and lease space to companies who wish to install their infrastructure within it. In contrast, the BADASS model simply allows EarthGrid to build the tunnel for clients paying per cubic meter, and clients maintain ownership and maintenance responsibilities.
This level of flexibility in business models adds a layer of customization to suit the unique needs of different projects. The models not only facilitate the construction of tunnels but also offer options for long-term partnerships and revenue-sharing arrangements.
Regulatory Approvals and Expansion Plans
EarthGrid’s strategic approach includes obtaining telecommunications utility status and a Certificate of Public Convenience and Necessity (CPCN) in 37 states, with plans for further expansion. This strategic positioning enhances the likelihood of obtaining Right of Way (ROW) permits, a critical component for projects involving underground conduits and utility lines. CPCNs can empower EarthGrid in negotiations with state departments of transportation, for favorable considerations in ROW access.
Depth Challenges and Cityscapes
The unique challenges presented by cityscapes, including the depth of storm sewers and the unpredictability of municipal infrastructure, necessitate nimble solutions. Municipalities often lack accurate records of storm sewer locations, making it challenging to plan around these obstacles. EarthGrid addresses this challenge through the use of ArcGIS solutions for co-location to map the underground landscape. EarthGrid’s plasma drilling technology proves to be more nimble in terms of turning radius, with a range of 6 to 8 meters, allowing it to maneuver through tight spaces in urban environments.
Personnel Safety and Environmental Monitoring
Safety is a paramount concern during tunnel-boring operations. EarthGrid implements strict safety measures, prohibiting any personnel from entering the tunnel while the tunnel-boring robot is in operation. Access can be provided through vertical shafts, ensuring a safe entry point for maintenance and emergency situations.
The use of electric carts for maintenance purposes minimizes the need for human presence within the tunnel during operations. Additionally, noxious gasses generated during the plasma drilling process are continuously monitored to safeguard personnel health and well-being.
Waste Management and Environmental Impact
One significant advantage of plasma drilling over traditional methods is its eco-friendly approach to waste management. Unlike horizontal directional drilling (HDD), which utilizes lubricants and generates wastewater, plasma drilling produces spoils consisting solely of rock. This eliminates the need for expensive wastewater transport and presents an opportunity to reuse the rock spoils. The repurposing of spoils into sand for shotcrete and concrete mixtures contributes to the construction industry, providing a sustainable solution for road and infrastructure development. The absence of harmful drilling chemicals further minimizes the environmental impact, aligning with EarthGrid’s commitment to responsible and sustainable construction practices.